At HCC, we don’t just manufacture complex steel fabrications and assemblies: We engineer them to perfection, delivering unmatched quality and precision that meet and exceed the unique demands of OEMs. With over 140 years of combined experience, our skilled professionals have a proven track record of delivering quality results for our partners.
HCC provides a complete range of complex steel fabrication and assembly services that cover everything from design and engineering to custom fabrication, simple steel fabrication, welding, painting, finishing, and assembly. We are dedicated to delivering quality workmanship and use advanced equipment and techniques to ensure accuracy and precision in all our projects. Our stringent quality control processes guarantee that our clients receive exceptional results and the highest level of satisfaction.
customized complex steel fabrication
We understand that every project is unique, and that’s why we offer customized complex steel fabrication and assembly solutions tailored to your individual needs. Our team will work closely with you to understand your specific requirements and design a solution that meets your needs and exceeds your expectations.
With a long history in the agricultural industry, we have also worked with clients in various other industries, including construction, manufacturing, and more. We are proud of our reputation for delivering quality results on time and within budget.
Don’t settle for anything less than exceptional. Choose HCC for your complex steel fabrication and assembly needs. Get in touch with us today, and let us help you bring your project to life!
complex steel fabrication Capabilities
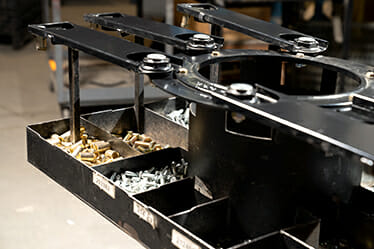
Efficient Flexible Assembly
By offering assembly stations for plastic, steel, electrical components, actuators, and seals, HCC can handle a wide range of products. This flexibility allows us to adapt to changing market demands and offer new products or services, streamlining the manufacturing process by providing separate workstations for different components. This allows our workers to focus on specific tasks, reducing errors and increasing efficiency. As a result, we can produce products at a faster rate and with greater accuracy.
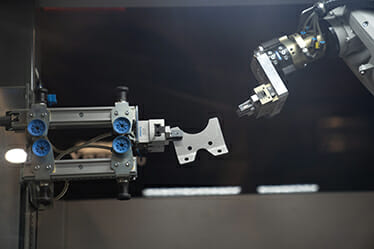
Diverse Capabilities
With continued re-investment, HCC continues to upgrade our facility, adding key automation and new equipment to be able to continue to handle any need of our customers. This flexibility allows us to adapt to changing market demands and offer new products or services.
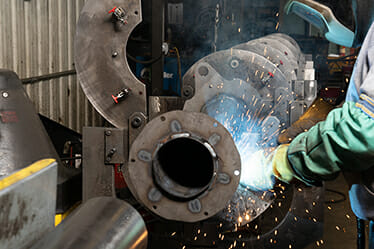
High-Quality Welding
HCC’s High-Quality Welding is hinged upon the experience and skill, expertise and knowledge of our tenured welders that is required to execute precise and accurate welds. Secondly, the quality of welding equipment and tools used by our company are vital in achieving high-quality welds. The use of proper and well-maintained equipment allows us to adhere to welding standards and codes, which ensures that the welding process is carried out according to industry regulations, resulting in safe and high-quality welding. Finally, our company uses high-quality materials, ensuring that the welds are strong, durable, and meet your specifications.
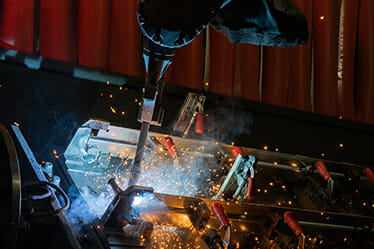
Multiple Robotic Welding Stations
Robotic welding offers many advantages, including improved precision, speed, and consistency. Having multiple robotic welding stations that can handle carbon steel, galvanized steel, and aluminum, with a 1100 lb capacity, provides HCC with increased production capacity and the ability to handle a range of materials. Our robotic welding stations can operate continuously, resulting in faster turnaround times, higher efficiency, and more consistent results.
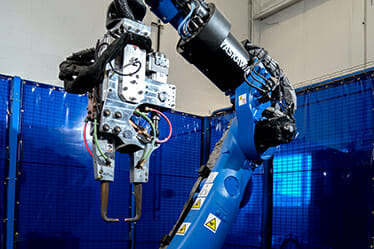
Automated Spot Weld Stations
Automated spot welding can produce a large number of welds quickly and accurately. Automated spot welding also reduces the risk of human error, resulting in consistent, high-quality welds.
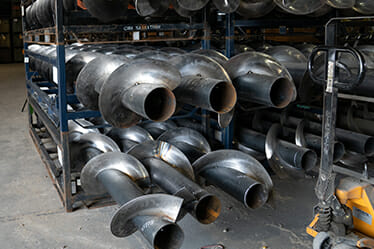
JIT Practices
Just-in-time (JIT) practices, including sequence direct to customer production line, help you reduce inventory, save money, and minimize lead times. By producing products only when needed, you can reduce the risk of excess inventory, prevent waste, and lower costs.
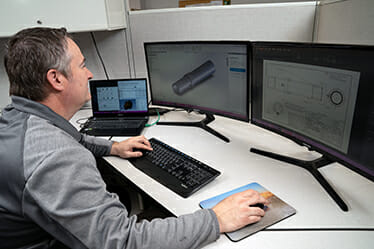
In-House Engineering
Our in-house engineering capabilities, including product design, design for manufacturing, fixture design, and tooling design, can help us partner with you in producing products that are more efficient, cost-effective, and tailored to your exact needs. This can result in a competitive advantage and improved customer satisfaction.
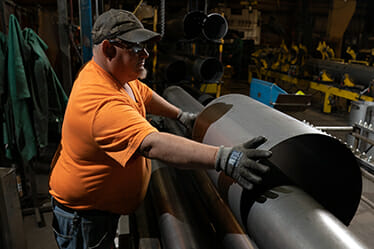
Rolling Machine Operations
HCC’s rolling machine operations offer versatility in handling various materials up to 10 GA and 12’ in length, enabling a broader range of projects and customers. It increases efficiency by handling long and thick materials for faster turnaround times, and its precision ensures superior quality with uniform and accurate rolling for projects that require a specific level of precision and consistency.
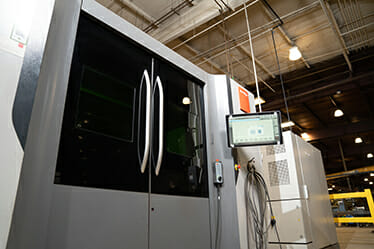
Laser Cutting
HCC’s Bystronics 6Kw Fiber Laser and Trumpf 4Kw CO2 Laser offer high-quality and efficient cutting capabilities for a wide range of materials and applications. The Bystronics 6Kw Fiber Laser offers high-precision cutting and high-speed cutting capabilities on materials up to 1″ thickness, with a large sheet size of 60″ x 120″ and an automated loading/unloading system. The Trumpf 4Kw CO2 Laser provides high-quality and high-speed cutting capabilities on materials up to .5″ thickness, with a large sheet size of 60″ x 120″.
HCC’s CNC Plasma Tube Cutter provides high-quality and versatile cutting capabilities for round, square, and rectangular tubing. It can cut through various materials, including steel, aluminum, and stainless steel, with precision cutting technology and a large cutting capacity of tubing up to 6″ in diameter and up to 4″ square and rectangle tubing with a thickness of up to 5/8″. With its automated cutting capabilities, this machine offers increased efficiency and reduced material waste, making it an ideal choice for manufacturing, construction, and metalworking industries.
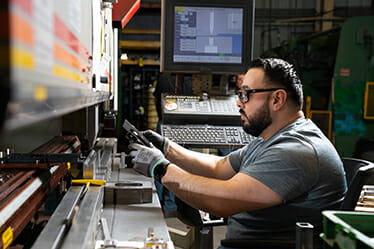
Press Operations
HCC’s wide range of press tonnages, from 22 to 250, and press brakes with a tonnage range of 60 to 350, and up to 12′ bed length, provide versatility for handling various materials and thicknesses. With the added value of a robotic press brake that has an 80-ton press and a robotic loader, we can offer precision and automation, reducing human error, improving production speed, and ensuring consistent and accurate bending, resulting in high-quality finished products.
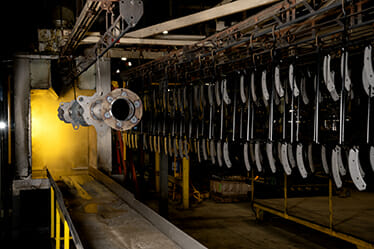
Dual Powder Coat Lines
HCC’s dual powder coat lines with a large paint envelope of 5’ x 5’ x 40’ enables us to handle larger parts, offer increased efficiency, and faster turnaround times for coating a larger volume of parts or products simultaneously. The ability to offer multi-color coating options and the 5-stage wash process ensures a superior finish. Moreover, powder coating is an environmentally friendly process that produces less waste and emissions.